More and more designers are designing for circular economies. Their focus tends to be on the production of mass manufactured objects. All aspects of the design process need to become circular if we are to mitigate design’s role in climate change as best as we can.This includes the basic tools of the trade, such as modeling materials.
For my industrial design masters thesis at the University of Illinois at Chicago, I developed plastic-free modeling materials. Cai Board can serve as a replacement for extruded polystyrene foam. Cai Clay is an air-drying clay that is an alternative to plastic-based clays.
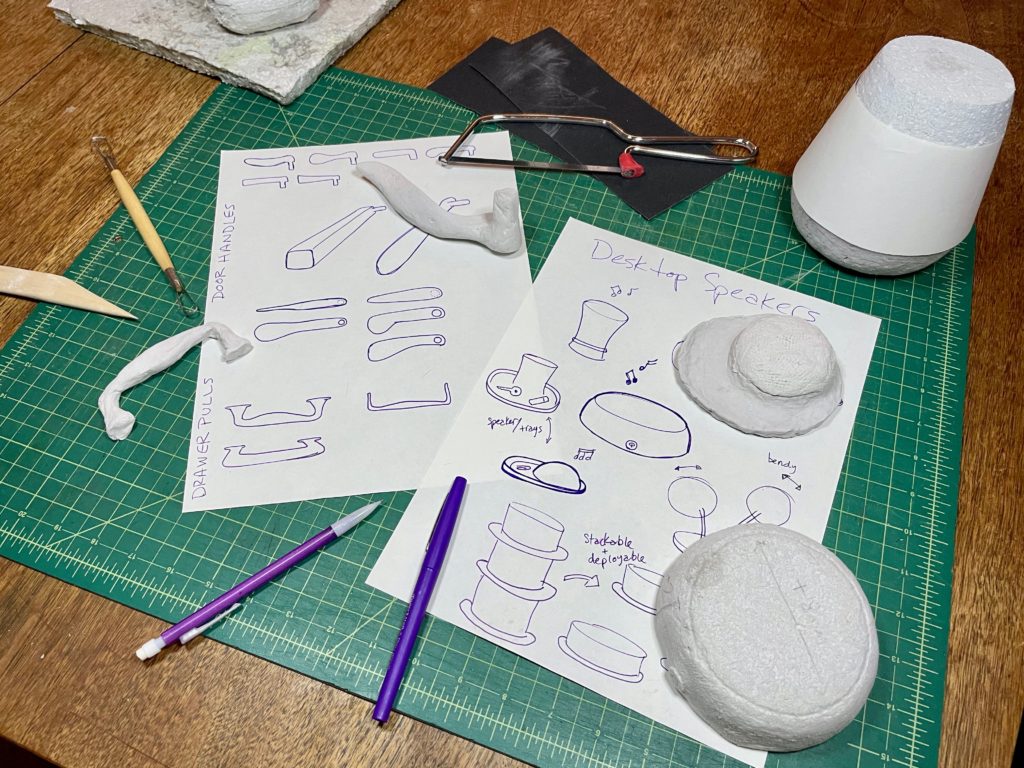
Changing our mindsets around disposability needs to start now, and it needs to start early in education. A common problem in teaching about the climate crisis is that it’s so big it can feel overwhelming. And so people get anxious, depressed, and do nothing. But research has shown that by first teaching children to appreciate nature in their own backyards, they’re better able to engage with the necessity of saving ecosystems halfway across the planet1.
If we teach young designers to value the tools of the trade through a sustainable lens, will they feel more empowered to make positive change? Will showing them small ways in which they can reduce waste help them see how they can have even larger impacts?
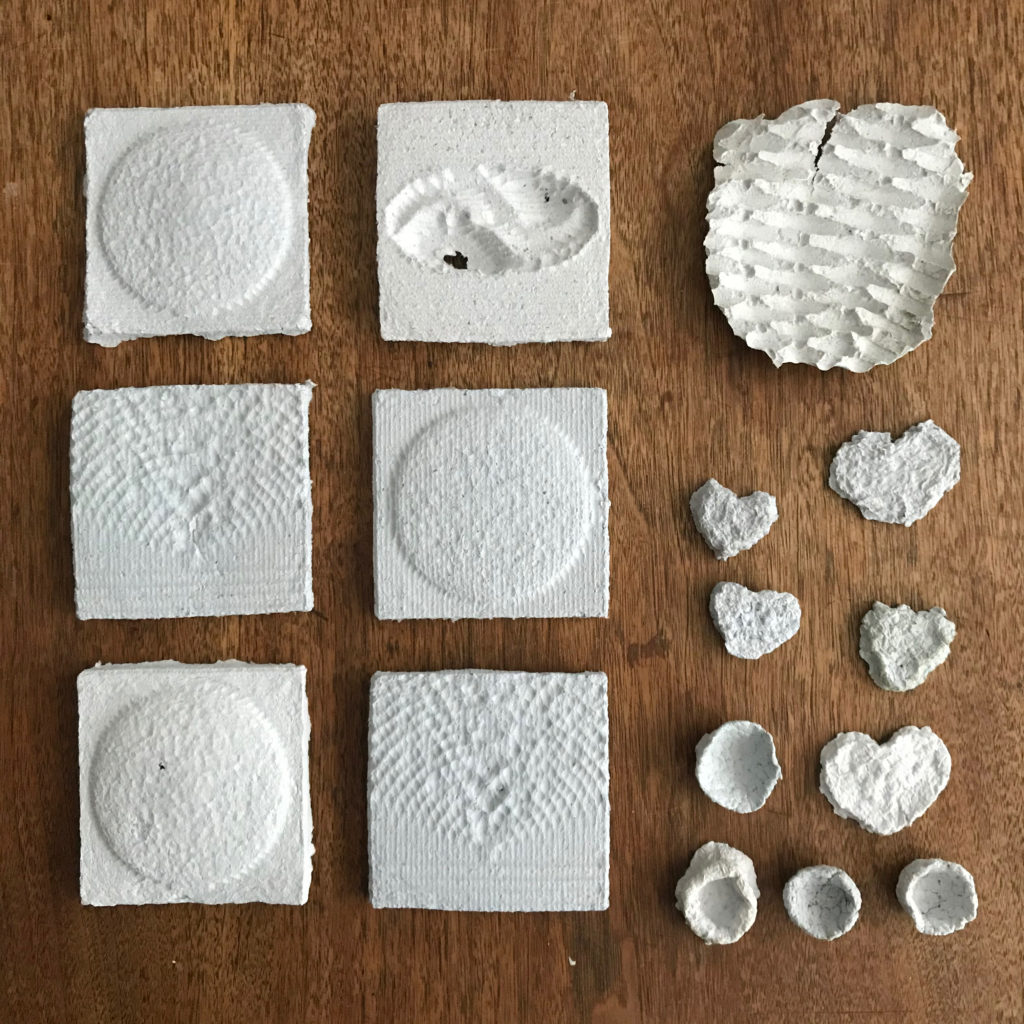
In design school, we carve up plastic foam for projects that will get thrown out at the end of every semester. Students often end up coated in foam dust, breathing in endocrine disrupting chemicals and synthetic estrogens. The microplastics that make up foam also get released into the environment where they pollute water and are eaten by animals. Plastic needs to stop being a standard modeling material.
In response to these issues of waste and the difficulties surrounding sustainability education, I developed the Cai Modeling Materials, alternatives to plastic-based modeling materials that are made using common household waste.
A student could make a batch of Cai Board at the beginning of a semester, use it to make their models, then recycle those models into new materials. They will save money (making design more accessible for lower income students), not inhale as many microplastics, put less waste in landfills, and hopefully reduce their eco-anxiety. All while learning more sustainable ways to design that they can bring with them to their professional lives. That is where I see one of the great potentials of this project, in helping train the next generations of makers to think more experimentally and to use regenerative materials.
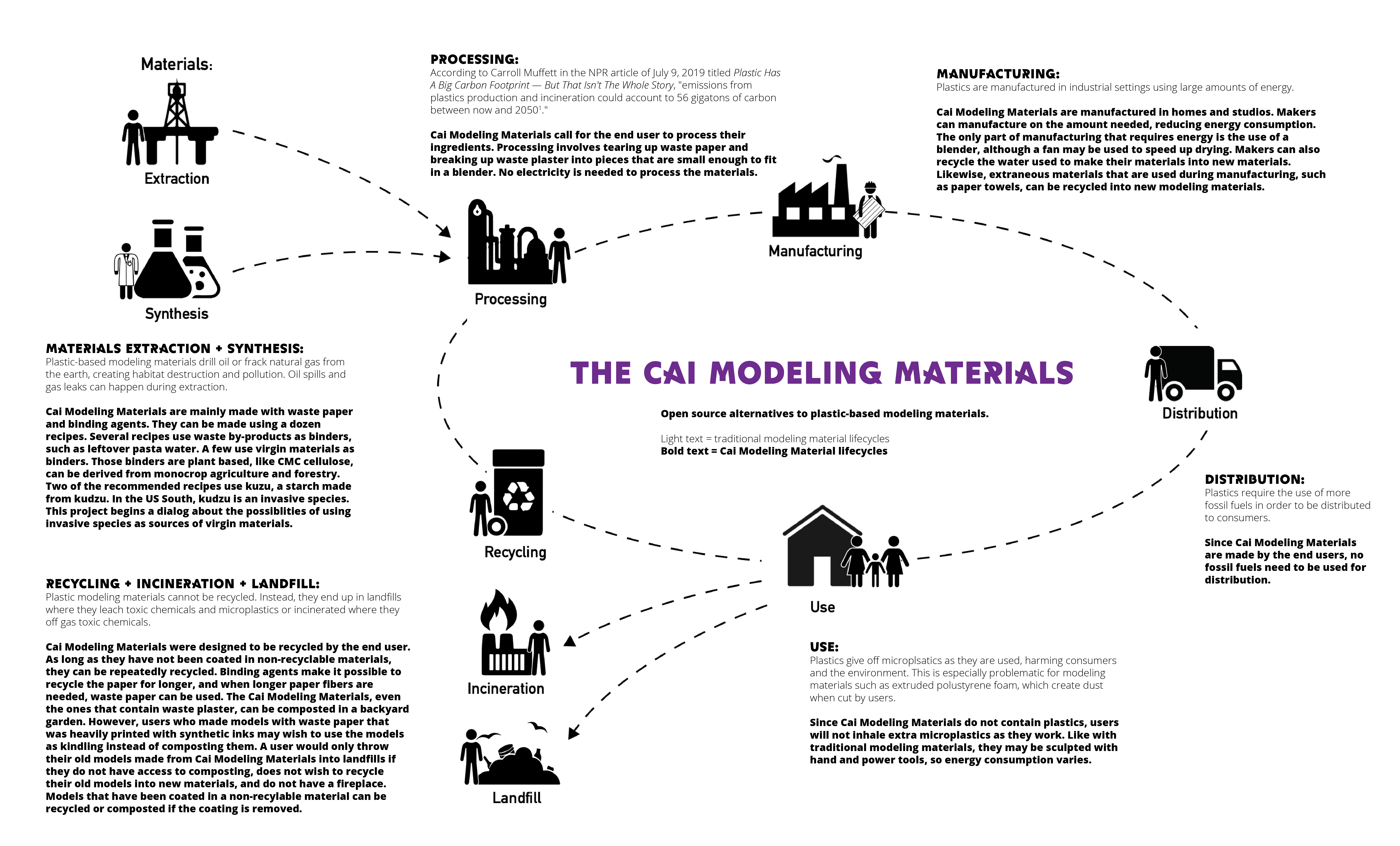
The Cai Modeling Materials are regenerative because they can be continuously recycled into new materials and even composted in backyard compost piles. Plaster, which is in Cai Clay, can even improve soil conditions2. Cai Modeling Materials’ ability to help reduce deforestation while amending soil makes them regenerative.
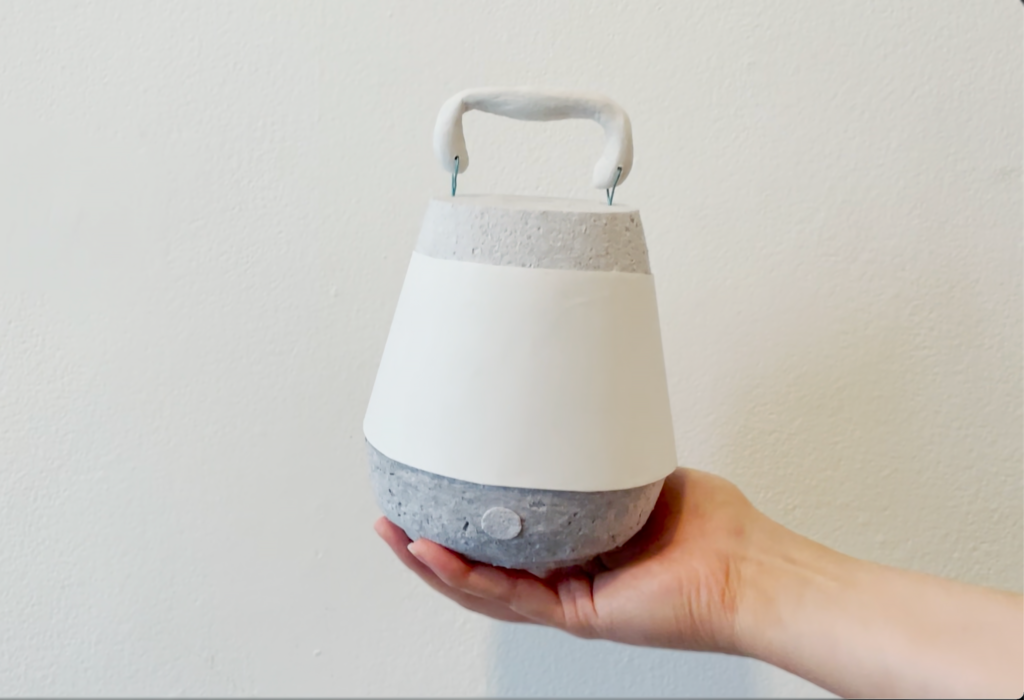
The invention of paper is attributed to Chinese court official Cai Lun in 105 AD. Earlier archaeological examples of paper have been found in China, though little is known about the craft of paper making prior to Cai Lun. That is why these modeling materials are called Cai Clay and Cai Board, to not just honor the history of paper but to connect prospective paper makers to its millennia-old history. To remind us all that if we want the human race to survive for millennia more, we need to embrace regenerative technologies, be they historical or brand new.
Both Cai Board and Cai Clay are good for subtractive making; the clay also works with additive making. And both materials can be combined. For example, the model lantern in the picture below was made with Cai Board for the body of the lantern and Cai Clay for the handle.
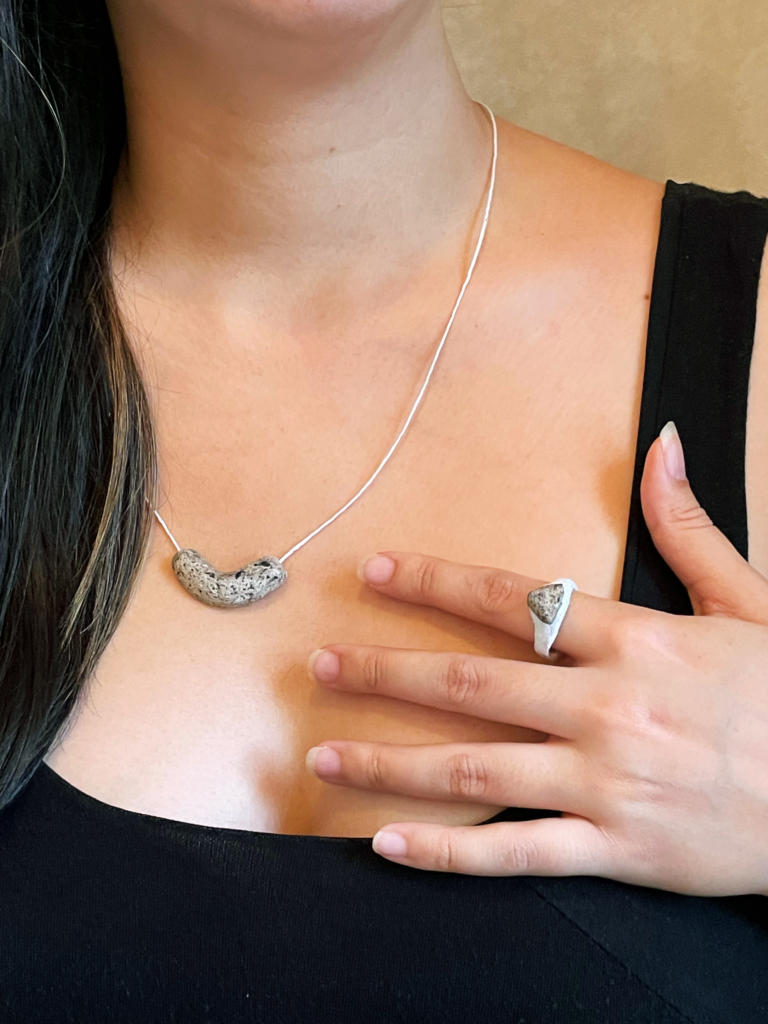
Since it is denser, Cai Board tends to hold up to falls, dents, and dings better than polystyrene foam. Its increased density means that it’s also heavier than a lot of polystyrene foam, which is useful for objects that benefit from feeling weighty, but not as useful for larger scale objects. While they can withstand the occasional splash, neither of the materials hold up well to getting very wet. In fact, getting them wet is the first step to recycling them.
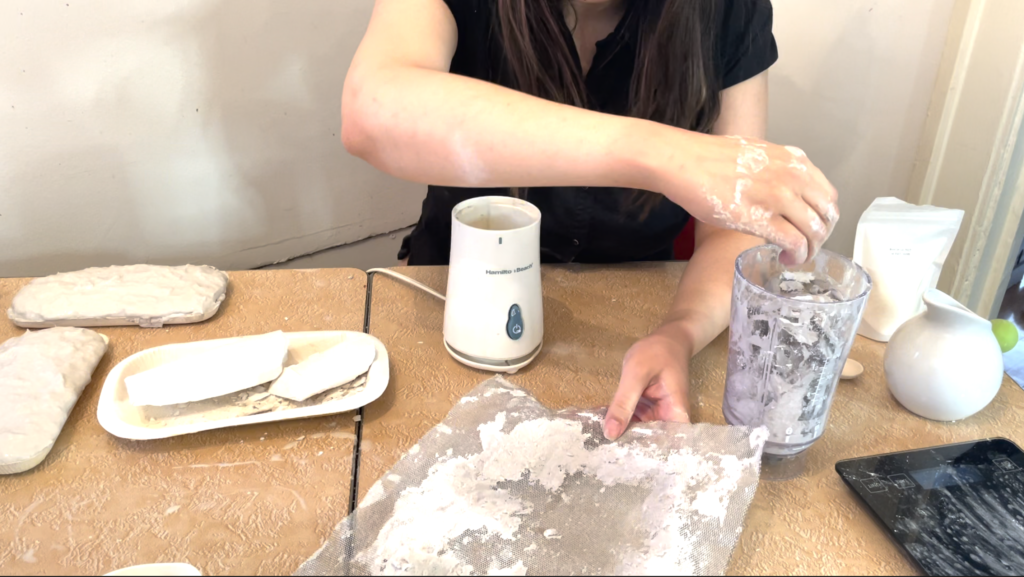
Manufacturing just one pound of uncoated, virgin computer paper comes at an environmental cost. And what is damaging to the environment is damaging to human health too. Humans, afterall, are part of nature. Uncoated virgin paper is commonly used by design students for sketching and often used for junk mail. One ream of paper weighs about 5lbs. Imagine what these numbers would balloon to when accounting for the 21.42 tons of paper that get tossed into landfills in the US in one year3.
1 lb of computer paper produces/uses:
- 4 lb of wood
- 9 lb of CO2
- 10.7 gal water
- .6 lb solid waste
- .45 lb hazardous air pollutants
- threatens 9 species
- 1.5 lb of ocean acidification
- .02 mg of mercury
- 1.6 μ of dioxin
The Cai Modeling Materials help address the problem of waste by being recyclable. Now, instead of throwing out dumpsters full of plastic models at the end of every semester, students can recycle those models into new materials for the coming semester. By recycling their models, they’ll also save money. Since the Cai Modeling Materials are inexpensive to create in the first place, this simultaneously aids the environment and students facing financial difficulties.
With a $12 bag of 100g of kuzu, you can make approximately 45-135 ft2 of 1/2” Cai Board. That will save 1.3 – 3.9 lb of paper from landfills.
With a $6 bag of 85g of CMC cellulose, you can make 4.5 ft3 of Cai Clay. That will save 1.6 – 2.4 lb of paper from landfills.
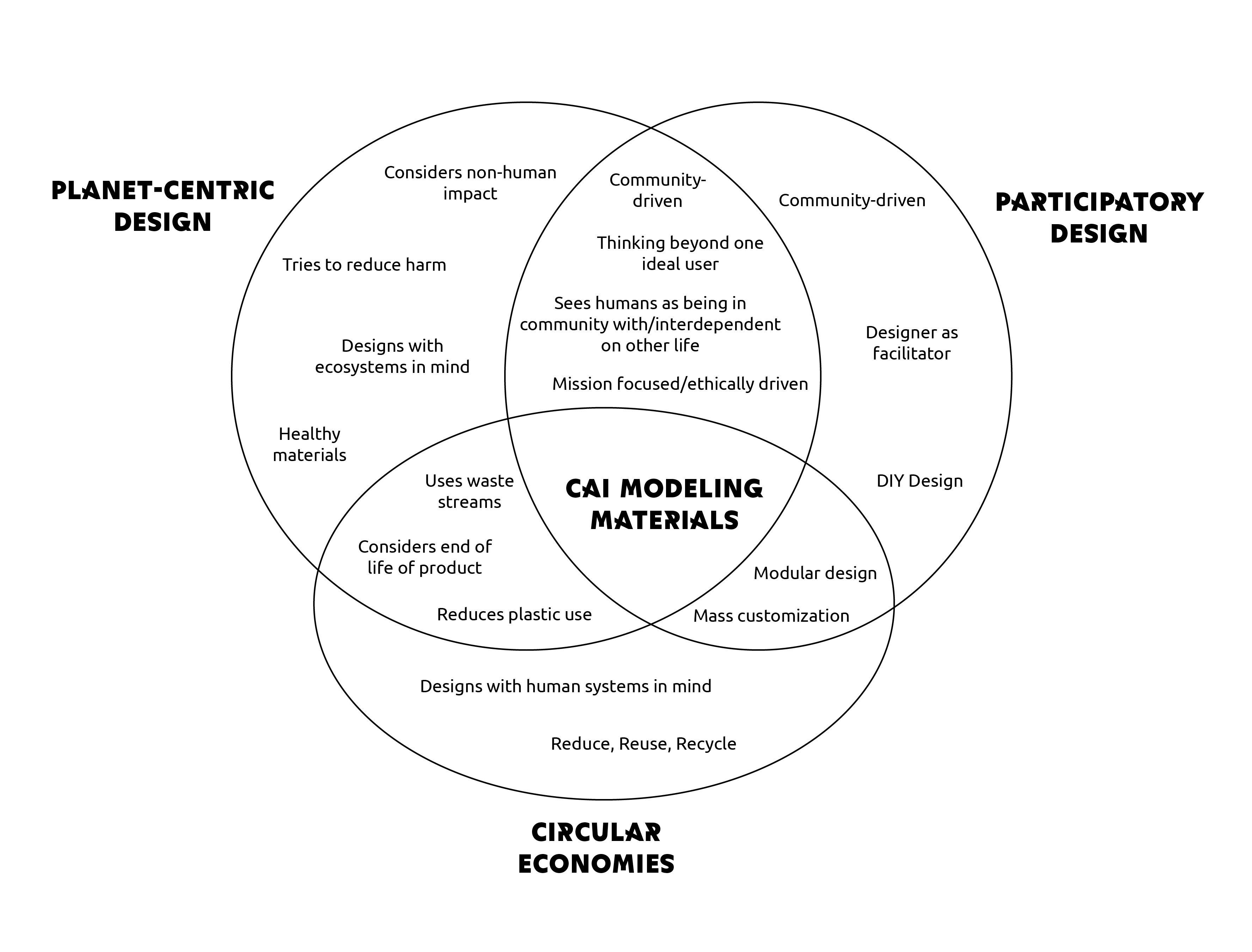
The ecological cost of the paper that is being recycled has largely already been spent. By giving that paper second, third, and fourth lives, we make the ecological cost stretch farther. We honor the deaths of the plants and animals that went into producing the paper. And now, that paper won’t end up in landfills where it would off gas chemicals like methane, which would compound the ecological cost of the paper. Instead, it can be recycled again, and even composted, returning to the soil without releasing huge amounts of methane.
My thesis is an attempt to help empower people to see how they personally can make change within a larger system. As designers, we are often implicated in mass manufacturing, and that is where the biggest reductions in greenhouse gas emissions need to take place. Showing designers personal changes that they can make to be sustainable in their creative practices can have a meaningful impact when they bring those changes to their professional lives.
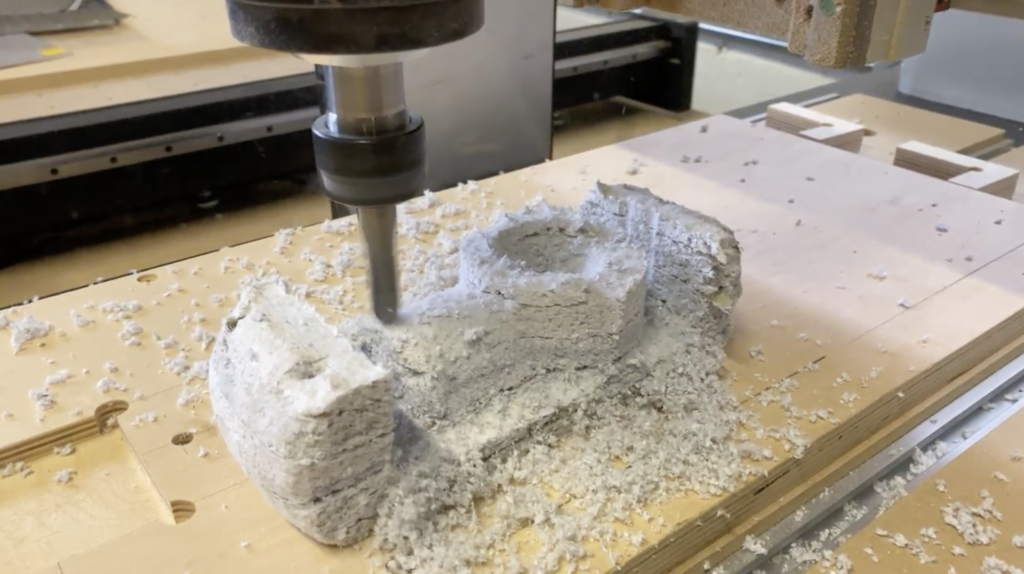
The Cai Modeling Materials page is the first of four parts of my Master of Design thesis.
See part two, Pasta Water for Designers.
See part three, Designing With Waste.
See part four, Criteria for Planet-Centric Design for an excerpt from my written thesis and a full bibliography.
Thank you to Ted Burdett for testing and taking the photo of the Cai Board on the CNC router.
1. Lopez, Barry, ed. “Beyond Ecophobia.” In The Furture of Nature: Writing on a Human Ecology from Orion Magazine, 1st ed. Minneapolis, Minnesota: Milkweed Editions, 2007.
2. “Wallboard (Drywall) Recycling.” Accessed March 30, 2021. https://www.calrecycle.ca.gov/ConDemo/Wallboard/.
3. Paper Calculator presented by Environmental Paper Network. “Paper Calculator 4.0.” Accessed May 5, 2021. https://c.environmentalpaper.org/individual.html.
Leave a Reply